Published date:
How efficiently do you heat your products?
In any process manufacturing business, the ability to heat up your products accurately and efficiently is key and always has a direct impact on the bottom line. Electric process heating can often provide the answer and is a compact and direct way to inject heat in a targeted way.
Manufacturing processes often use a multitude of heat sources to inject heat into or to cool their products. A common misconception is that the use of electric process heating solutions such as industrial immersion heaters and process flow heaters are an inefficient source of heating. This couldn’t be further from the truth with a sheathed heating element being around 99% efficient when it comes to converting power to heat. Combine this type of electric heating with immersion directly into a liquid and there’s nowhere for any losses to go but into the media you want to heat!
Smart Control – In most heating applications energy usage and process efficiency is a key requirement although one whose importance may be overlooked. Industrial electric heaters generally employ sheathed heating elements at the heart of their design. There will, more often than not, be an array or battery of heating elements and this is where control can be applied to provide smarter energy solutions. This can run from simply applying more accurate sensing and switching technology to the heater through to more complex cascade element controls. An example of this is to use either solid state switching or thyristor control on individual heating elements that make up a heater. This allows different heat output levels depending on the level of utilisation in a tank or flow in a pipe. Combine this with accurate temperature measurement and PID or three-term control (which is available in most stand alone or PLC controllers) and direct electric heating can become one of the most efficient ways to heat your product.
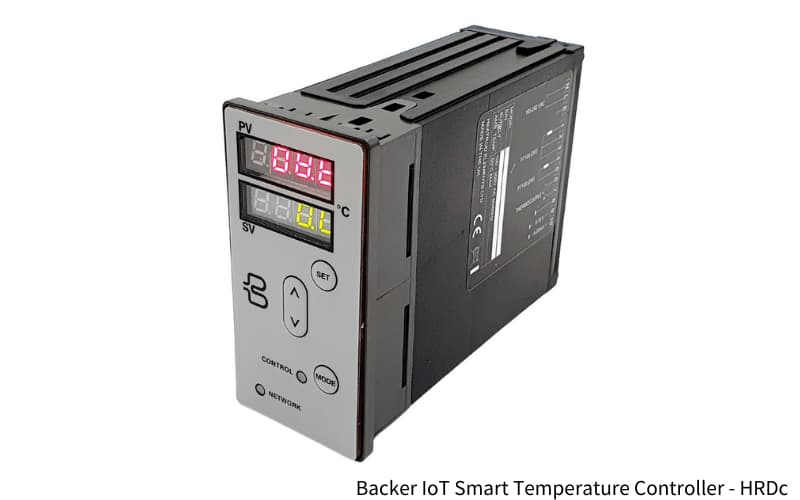
Our new Backer IoT Smart Temperature Controller (HRDc) has been developed to fill a gap in the digital control of our own heating products, allowing users to visualize and control energy usage and application temperatures remotely. Heating equipment will nearly always be the highest user of energy on a commercial or industrial site - active monitoring and management can quickly benefit the user through energy savings. Our Smart Temperature Controller is designed to be incorporated into integrated heating applications, built into our immersion heaters and also as a stand-alone panel mounted independent controller. The HRDc is designed to be fitted directly into your control or instrument panel with an easy to fit flexible housing. Both process and target temperatures can be easily viewed from the front screen and alterations to the set point can be made using buttons on the front panel. Click here for more details.
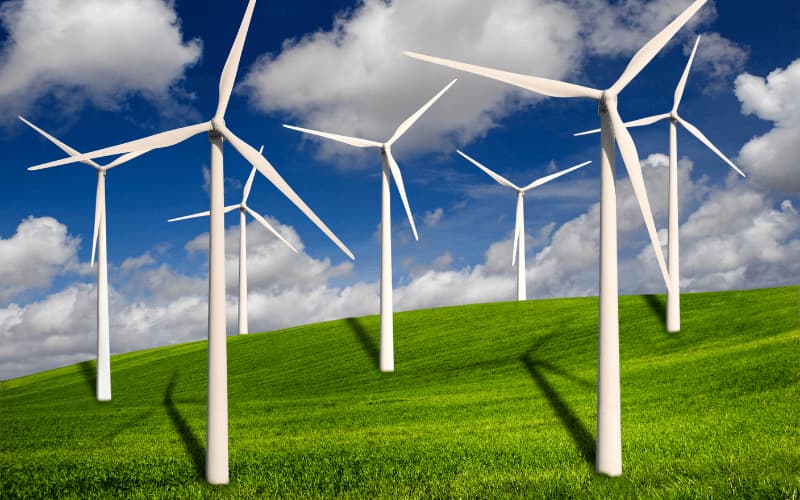
Just like the ingredients that go into any end product, no manufacturer wants to add any more energy than is required in order to produce their product. Combining the cost of energy with the drive towards net zero makes for a difficult set of criteria to meet. Electric heat is generally the cleanest form of energy at the point of use, but it is often not recognised as a clean energy because of the methods of generation traditionally associated with our electricity supply. The good news is that this is a fast-changing landscape and with renewable energy being 37.3%* of the UK’s generating supply in the second quarter of 2021 and with more end users considering renewable forms of micro-generation, the use of electric heating is genuinely becoming the cleaner choice.
For more information on industrial heating see our Industrial Heating Products
Alternatively, why not contact us to discuss your application.
*Figure taken from Energy Trends September 2021 – gov.uk